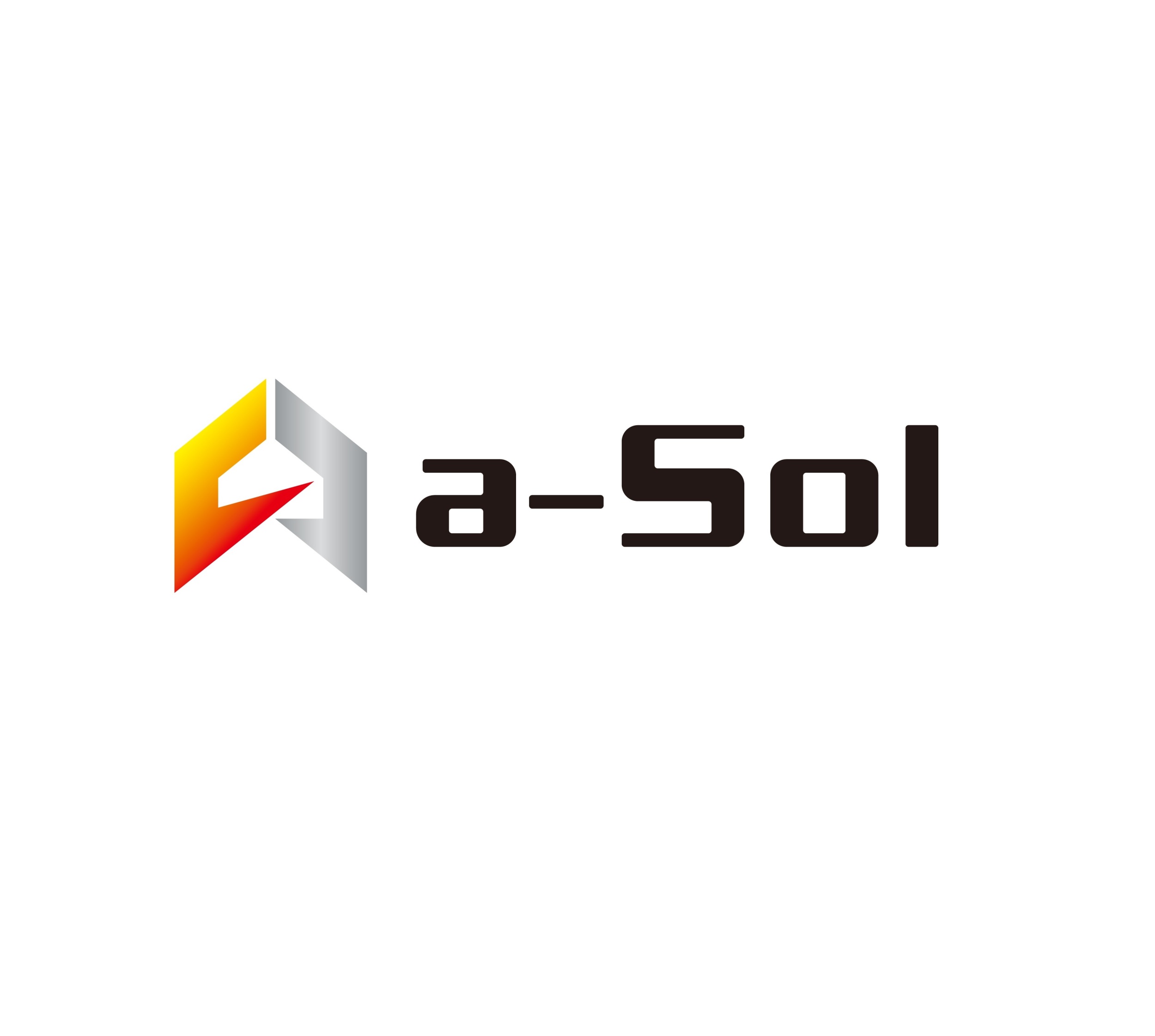
今回のテーマは
PDCAサイクルとSDCAサイクル?
です。
まずPDCAは仕事・プロジェクトを効率的に進める手順であり、
Plan(計画)
Do(実施)
Check(確認)
Act(処置)
という内容です。
多くの方がどこかでは耳にしたことがあり、仕事の基本として、有名なサイクルではないでしょうか?
そして、企業の運営もこのサイクルに沿って行われているので意識せずとも自らの仕事にPDCAのサイクルが根付いているという方がほとんどだと思います。
年度方針が決まり(Plan)方針から自分の部署、チームがやることが決まり(Do)、それに対して中間点検や結果確認があり(Check)確認結果に対して、対策や処置がなされる(Act)というように。
そしてよりブレークダウンされた自分の仕事に落とし込んでも、このサイクルに沿って運用されています。
なので日々仕事をしている方にとっては意識せずとも、実施し続けており体に浸み込んでいる内容だと思います。
では、これに対してSDCAとは何でしょうか?
それは日常的に繰り返される業務を維持管理する活動です。
Standardize(標準化)
Do(実施)
Check(確認)
Act(処置)
というサイクルになっています。
日常繰り返される業務を徹底的な標準化を実施し、生産現場でも事務作業でも、
誰が、いつやっても、決まった時間で、同じ成果(製品)ができるという標準を作り(Standardize)
それに従って仕事をし(Do)、
標準通り仕事をしているか確認することも仕事となっており(Check)・・・
前回話した管理者監督者の仕事、
それを守れていなければどうして守れていないか、
何がおかしかったのかに対し処置、対策をする(Act)という流れ
で進めます。
主にルーティン業務を円滑に回す仕組みとして導入されているのです。
このように見ていくとPDCAは企業活動の流れとマッチしており、自然と組織の各々に根付いていくサイクルですが
SDCAは企業活動のサイクルとは異なって日常維持管理がメインであり、
企業活動のサイクルに合わせて放っておいても根付くような仕組みではないのです。
(日常業務はSDCAで回すんだと宣言して初めて意識する)
大まかに言うと
PDCAは良い変化を生み出すサイクル
SDCAは悪い変化をさせず維持するサイクル
です。
企業は社会に対してよい変化を与え、価値を生み出すためにあるので、今年はこういう変化をしていくんだ!!と目標や方針を決め、運営していくのでPDCAがメインです。
しかし実際企業活動の中身を紐解いていくと、膨大なルーティン作業、同じ作業の繰り返しで構成されています。
その作業の一つ一つが劣化しないように、悪いものを流さないように、
誰がやっても同じ時間で同じ品質のものができるように徹底的にStandardizeすること
がリソースを無駄にせず、アウトプットにつなげるためには必ず必要です。
そして徹底した見える化(目で見る管理)、4Sや標準作業の話というのは、基準(Standard)を作ることを第1ステップとし、その基準から外れるも野に対してアクションを取っていく、というSDCAサイクルを回すためのものです。
SDCAサイクルは日常管理なのでカイゼンではないような感覚を持ちますが、
それは半分あたりで、半分ハズレです。
なぜかというと、ほとんどの企業、生産現場というのはStandardの作り込みができていないので、
実際に文書、数値として作成していくと、今までこんなに無駄なことをしていたのかと見えてくることとなり、
業務や作業の不要な部分の削除につながります。
今まで勘や経験で行っていた仕事がプロセス、手順を明確に分解することによって
標準がない時よりも工数低減につながります。
ここがスタートラインであり、その標準に沿って仕事をしてみてやりにくいところは変える。
標準が守れているかチェックしてみて守れていなければ、必ず守れない理由というのが出てくるのでその標準を再度見直す。
トヨタではこのように日常維持管理が行われていきます。
そしてカイゼン活動はそれができたうえでもっと良いものを、もっと安く、もっと早くというKPIを狙ってPDCAサイクルで実施していくのです。
- SDCA(基準を徹底し、日常維持管理による異常撲滅の仕組み)
- PDCA(目標に対してのカイゼン活動)
この2つを分けて考えることが大切なのと、あくまでも1が基本(前提)としてできていることで2の活動が活動前との比較可能な状態になり効果が出る活動ができると言えます。
トヨタがほかの企業と違うと思うのは、会社の方針や目標というものは毎年作成され更新されているのですが(PDCAサイクルに沿った目標)、
日々繰り返しの仕事、ルーティン業務、個人が行う仕事に対してもTPSの追求という明確な指針、目指す姿があるということです。
(SDCAサイクルの徹底)
TPSの考え方が従業員に浸透しているので、目標に対して取り組んで成果を出す!というよりは、毎日のルーティン業務に対してその考え方に近づくように、この取り組みはその考え方に反していないかということを日々照らし合わせながら仕事をしているという感じです。
どの従業員も基本的にはSDCAが自分達の毎日の仕事です。
基準から乖離する異常があると、異常が起こる原因、異常が二度と起こらないようにする対策をする。
これが基本の仕事。
そしてそれに加えてカイゼン活動(やりにくい作業、ここがもっと楽になればよいのに、もっと早くできないか?)という問題意識に対して、PDCA型の問題解決に沿って進める。
なので、日常管理で異常だらけだと、カイゼン活動に使える時間が無くなります。
それは自分の業務範囲のSDCAが徹底できてない証拠ともなります。
(Standardの作り込みができていない)
そして優先順位はあくまで日常業務→カイゼン業務なのです。
ちょっとややこしいので自分のとりくみ姿勢としては標準が既に張り巡らされた職場なので、
異常が発生しているか確認しその異常に対して原因追及、対策を打つのが日常維持管理。(SDCA)
異常がなく、一見スムーズに回っているように見えても標準や今までのやり方をよりよいものにしていくのがカイゼン活動(PDCA)
という様に分けています。
しかしやはりその大前提は標準(Standard)があることです。
さきほども書いたように、まったく標準がない現場、業務はこれをしっかり作ることで、無駄が浮き彫りになる効果があります。
ルーティン作業なら特にぼんやりとした手順でも、取り組む順番はバラバラでも人間は器用なので普段やっている慣れのおかげで大体同じ結果が出るように見えますが、
標準を作るという科学的態度、意識で自分の仕事を分解することによって初めてムダに気付ける機会になります。
今回は、
*日々の仕事の大部分である日常維持管理業務をSDCAサイクルで回すということはPDCAサイクル(企業活動)と違い放っておいても身に付き、意識できることではないということ。
*だから従業員にこれが仕事なんだと意識させ、根付かせていくことが大切だということを
長々と書かせていただきました。
その最初のステップが目で見る管理のできる職場づくり(見える化)や4Sの推進につながります。
これを分けるのはSTEP1の段階でどれだけ多くのメンバーが目指すその先をはっきり理解しているか、(させているか)そしてこの活動は自分とつながっている取り組みなんだな、と参加意識が生まれているかです。
(こいつはと思う部下には、構想段階で早めに入って議論しておく)
本日はSTEP1の問題の明確化にあたりどうしてその問題に取り組むか?その先に何を目指すの?ということを組織で考えることの大切さ
またカイゼン活動に取り組む管理者、リーダー、メンバー間の優先順位見ている視点を合わせていく作業としてSTEP1が必要ということを長々と話させて頂きました。
今回も長々とお付き合い頂き、ありがとうございました!