こんにちは!
カイゼン研究会の宇賀です
突然ですが…
実はトヨタ生産方式(TPS)には体系的に学べる教科書がありません。
大学などでも事例としては存在しておりますが、理論として学べるようなモノではないのです。
しかし、オイルショック以降世界に注目を浴び、アメリカの研究者が見学やインタビューをもとに研究を重ねたものがリーン生産方式となって世界の工学部や経営学部で教えられています。
そんな成り立ちで世界に広まっているので中には誤解もあります。
リーンという意味はムダの無いという意味で、TPSの2本柱で言うところのジャストインタイムに重きを置いた翻訳です。
そして意外なことに、リーン生産方式の中には人偏のついた自働化の概念はほとんど触れられておりません。
自働化は単純に品質管理手法として扱われていることが関係しており、品質管理の科学的手法、シックスシグマなどはアメリカで発展しているので、自働化を特段入れなくてもよいのだという理由があります。
それに加え「自働化は人のチェックを重視するのでしょ?もっと科学的にしないとだめだよね。」という二つの誤解から来ているようです。
本来は異常があれば止める、止まるというのは単なる品質管理のためだけではありませんし、人のチェックで止めることを推奨している訳でもありません。
しかし、異常発見から従業員が問題解決するという考え方がアメリカの工場労働者に対するイメージや文化と大きく異なるため、誤解のあるまま伝わった、もしくは使えないと判断されました。
(IoTの発展などで今は見直されております。)
そのように世界に広まり運用されている中で、特に他国で疑問に思われている部分は、ボトルネックについての考え方です。
ボトルネックというのは製造業で簡単に言うと工程全体の中で処理が一番遅いところです。
アメリカでは小説「ゴール」でおなじみのゴールドラット博士の制約理論(TOC)が有名です。
ボトルネック(制約)を見つけ、カイゼンし、その他の工程はすべてボトルネックの工程に合わせて動かす。
その他の工程をカイゼンしたところで意味はない、やらなくてよい。
大まかに言うとこういう合理的な考え方が主流です。
なので、海外から日本のトヨタ生産方式やカイゼン活動を見ると、全従業員がそれぞれの職場でカイゼンを出したり、創意工夫を出しているのは非合理的に見える。
集中と選択ができていないと思っている人もいるということです。
これは面白い部分で、人材育成の観点やトップダウンで短期的な成果(欧米型)、ボトムアップで長期的な成長(日本型)などの文化の差が出ているように感じます。
人材育成面だけでなく、効率への影響もあります。
工程のサイクルタイムというのも、ほとんどの場合は確定しているものではなく、10秒と思っている工程でも実際は7秒~14秒が確率的に変わるということが多く、工程が長くなればなるほど理論上と実際でかなり影響が出ます。
全行程、各自が改善を行うというのは非合理にも見えますが、制約理論だと重視しない、そこのばらつきも許さない徹底さも兼ね備えているのです。
しかし、このボトルネックで少し見えるように、全体から俯瞰的に見てどこが弱いか特定して、最大の効果がある部分に取り組む、という全体最適の考え方が欧米に比べ日本では弱いというのが通論です。
各自が部分最適を追いかけてしまい各々は効果が出たと思っているが、全体で得になっているか?ということを測定、評価がされずに終わるということが多いです。
これはすごく大切で、知らず知らずのうちに部分最適に陥るということは必ず起こります。
なぜなら、見る範囲を広げれば広げるほど最適の意味が変わってしまいますし、関連する部門や組織が増えてしまうので見切れないということが起こります。
これは日々のカイゼンと、全社プロジェクトとしてやるような活動に分けて進めていくことが必要です。
ある部門のカイゼン活動に期待をしているだけでは、全社視点での全体最適をかなえるような活動やテーマは出てこないのです。
この部分最適、全体最適で有名な例が建機メーカーのコマツです。
建機をインターネットにつなぎ1台1台の稼働や位置情報をモニタリングできることで大成功しました。
(2000年前後のことなので取り組みの速さがすごいです)
さらに発展させ、位置情報や設計情報、建機の油圧から効率的に土を盛るにはどう動けばよいかを遠隔操作でサポートできる建機まで開発しました。
その結果、建機を使った作業は1.5倍以上の効率化を実現したのです。
しかし、実際に購入した現場ではそこまでの成果が出ていないことがわかりました。
原因は工程の中にありました。
(1)掘削場で土を掘る
(2)建設現場に土を運ぶ
(3)建設現場で土を盛る
コマツの建機は(3)で使われていましたが、土をいかに効率よく盛れるようになっても(2)の効率が上がらない限り、運搬される土のスピードが追い付かないということがわかったのです。
これは、今までの自社の範囲を超える視点で見たときに
部分最適になっていないか?全体最適は何か?ボトルネックはどこか?
が変わったということです。
そこからコマツは
・土の必要量はどれくらいか?
・トラックが何台必要か?
・最適な運搬ルートは?
などなど、各課題に対してドローンやAIなど最新技術を駆使し、ボトルネック解消のために今までの建機という範囲を超えたサービスを提供し始めています。
長々と書きましたが、このボトルネックに対する意識が部分最適に陥ってないかというのは、トヨタ生産方式ではなかなか体系化できていない部分であります。
(もちろんモノと情報の流れなどのツールはたくさんあるのですが)
この考え方を取り入れてボトルネックを重視したカイゼンプロジェクトができているか、1度チェックする機会を入れてみてはいかがでしょうか。
今までのカイゼン活動を変えるきっかけになるかもしれません。
最後までお読み頂きありがとうございました。
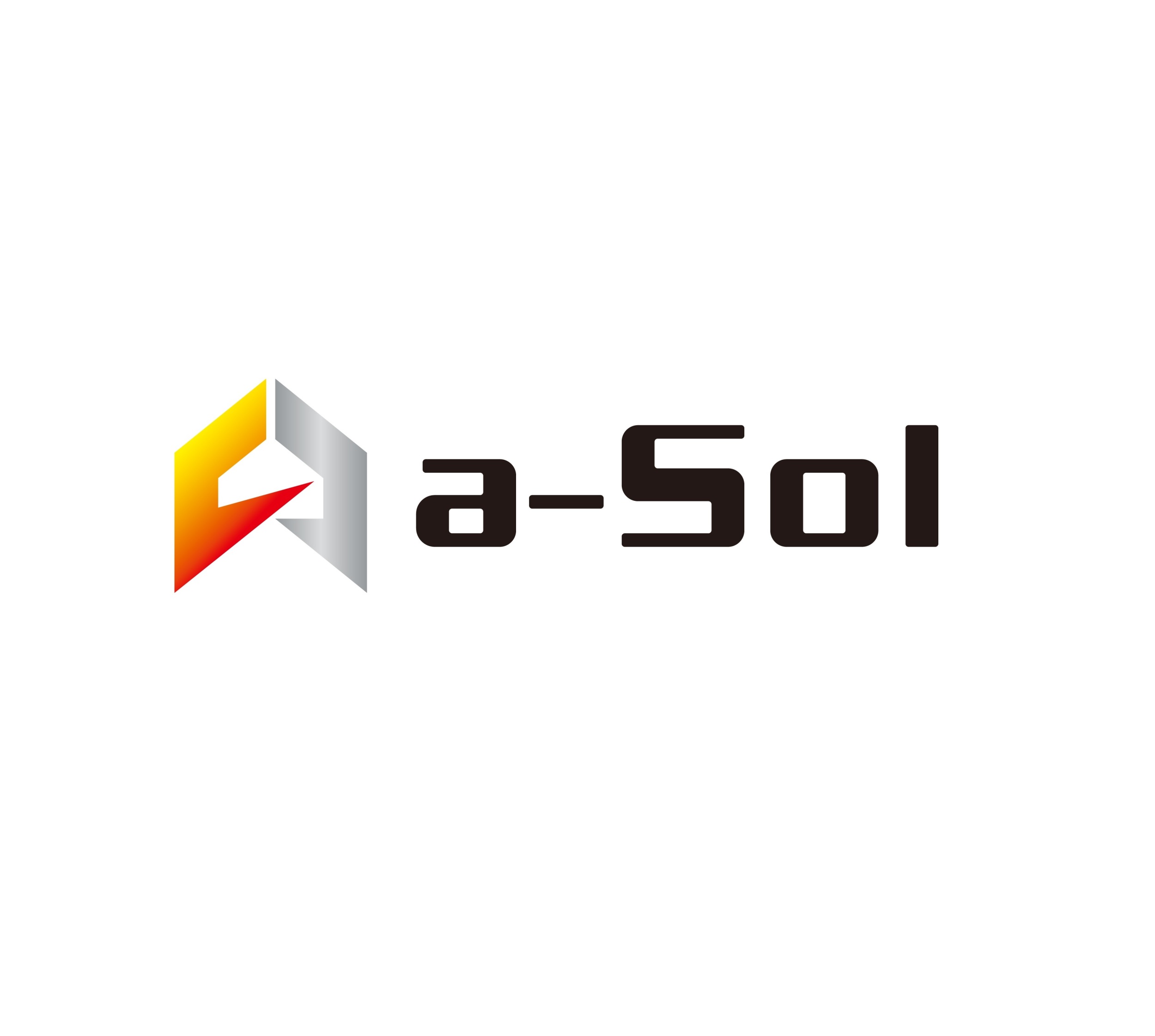