こんにちは!
カイゼン研究会の宇賀です。
今回のテーマは生産現場の実力は「仕掛け」で決まる??です!
仕掛品という言葉は工場ならおなじみの言葉ではないでしょうか?
生産を開始してから、完成品になるまでの間のモノという扱いです。
この仕掛品が多いということは工程間の在庫が増えてしまうので、会社のキャッシュフローを圧迫する原因となります。
今回扱う「仕掛け」というのは、生産着手という意味で、実際に現場で従業員が生産活動をするときに何をどんな順番でどれだけ作るか?という情報を示しています。(生産指示情報)
この仕掛けこそが、産業革命から続く、生産性の追求において過去(産業革命以降~フォード生産方式)と現代(トヨタ生産方式を代表とする現代の生産システム)を分けるものでもあります。
自分の工場の仕掛けはどうなっているか?
過去の方式のまま止まっていないか?
を考える材料になればと思います。
ではまず、仕掛けの重要性についてまず説明していきます。
よく聞かれる「生産計画と何が違うの?」という質問があります。
お客様からのオーダー数量をもとに製造部が作る順番まで明確に指示している生産計画だったら生産指示情報、すなわち「仕掛け」になっています。
しかし、ほとんどの場合、生産する際に使用する生産指示情報(仕掛け)は生産計画通りにはなっていません。
なぜかというとオーダーの数量、納期通りに製造が作れることはほぼなく、段替えや、治具交換など生産する品番を切り替えるたびにロスが発生する状況がほとんどなので、
実際は同じ品番はまとめて作ったり(ロット生産)しており、生産計画と実際の仕掛けは異なることが通常です。
生産計画を作る人が製造工程に精通しており、どの順番でどれだけ作るかまで決定できることは少なく、
実際の運用は生産計画を受け取った製造部が自分の工程の状況を考慮し、
順番を考えて作業者に生産指示を出している状況です。
なので、上層部からするとこの仕掛けというのはブラックボックスになっています。
(どういう根拠で生産開始しているのかが分からない)
ここがブラックボックスになると、製造部のやりやすいように生産し、
監視機能がないので欠品を防ぐために、前もってたくさん作ろう!となっていき、
結果的に在庫が増えていくという事態に陥ります。
しかし、そこを何とかしようにもこの仕掛け、生産指示の方法、ロジックを知っているのは製造部だけなので手が出せないという悪循環が起こるのです。
なので、この生産指示(何をどんな順番でどれだけ作るか?)が生産計画から誰がどのように決めているのか?を調査することが1歩目となってきます。
製造部の経験や頭の中だけにある計算で作る順番を決めていることが多く、ミスが起こっていてもわからない部分なのです。(知らぬ間に在庫増加を引き起こします。)
次にトヨタの場合はこれをコントロールするためにかんばんというツールがあります。
各工程ごとに完成品が次の工程に運ばれた数だけ仕掛けかんばん(生産指示情報)が外れ、その仕掛けかんばんの数だけ生産着手していきます。
仕掛けかんばんというものが生産する権利となっているので、かんばんが外れたり、新たに増えない限り作りすぎることができないように管理しているのです。
もちろん、単純に説明してきましたが、オーダー量の多い定番品番、少量品番等を考慮して数パターン、生産指示ルールを作っていることがほとんどです。
・単純にかんばんが外れた順番に作ろう
だったり
・かんばんが100枚たまったら作ろう
品番によって
■定量不定期(一定の数溜まったら作る)
■定期不定量(一定の時間で外れた看板分を作る)
などなど。
こういった考え方を組み合わせたりしながら生産指示(仕掛け)のルールを決めているので、
製造部のみのブラックボックスにならないようになっているのです。
かんばんについてはあくまで例で出したのですが、今回言いたかったのは
「仕掛け」、生産指示情報がどうなっているか把握しておかなければ作りすぎ、在庫、長いリードタイム(早めに生産開始してしまっている)といった問題に切り込むことができない、
ということでした。
「うちの工場は生産計画に基づいて生産しているよ!仕掛けや生産指示情報なんて難しいことはしていないけどな。。」
と思っている方は多いですが、この仕掛けというのはどんな工場にも存在しています。
中国では特に、現場管理者の頭の中だけにあるということが多く、盲点になりがちなのです。
(頭で考え、口頭で生産指示を作業員に出したりしています。)
この仕掛け情報のコントロールというのがトヨタ生産方式のような現代の生産システムの大きなターニングポイントです。
産業革命以来、テイラーの作業研究やマニュアル化、仕事量管理(今でいう標準作業の考え方)
フォードの分業化、流れ作業化(今でいう工程の流れ課)
というのはトヨタ生産方式以前にすでに確立されてきたものですが、
この生産指示という情報をルール化しかんばんというツールを使って「動く情報」として扱っているのが、
トヨタを代表とする現代の生産方式となっています。
(今までは生産計画という固定の情報のみだった)
なので、この仕掛けという部分に関して自分の工場は今どうなっているか?
を把握することは手軽で非常に大切な第一歩となります。
(産業革命当時の100年以上前のシステムで止まっているかもしれません。。)
最後までお読みいただきありがとうございました!
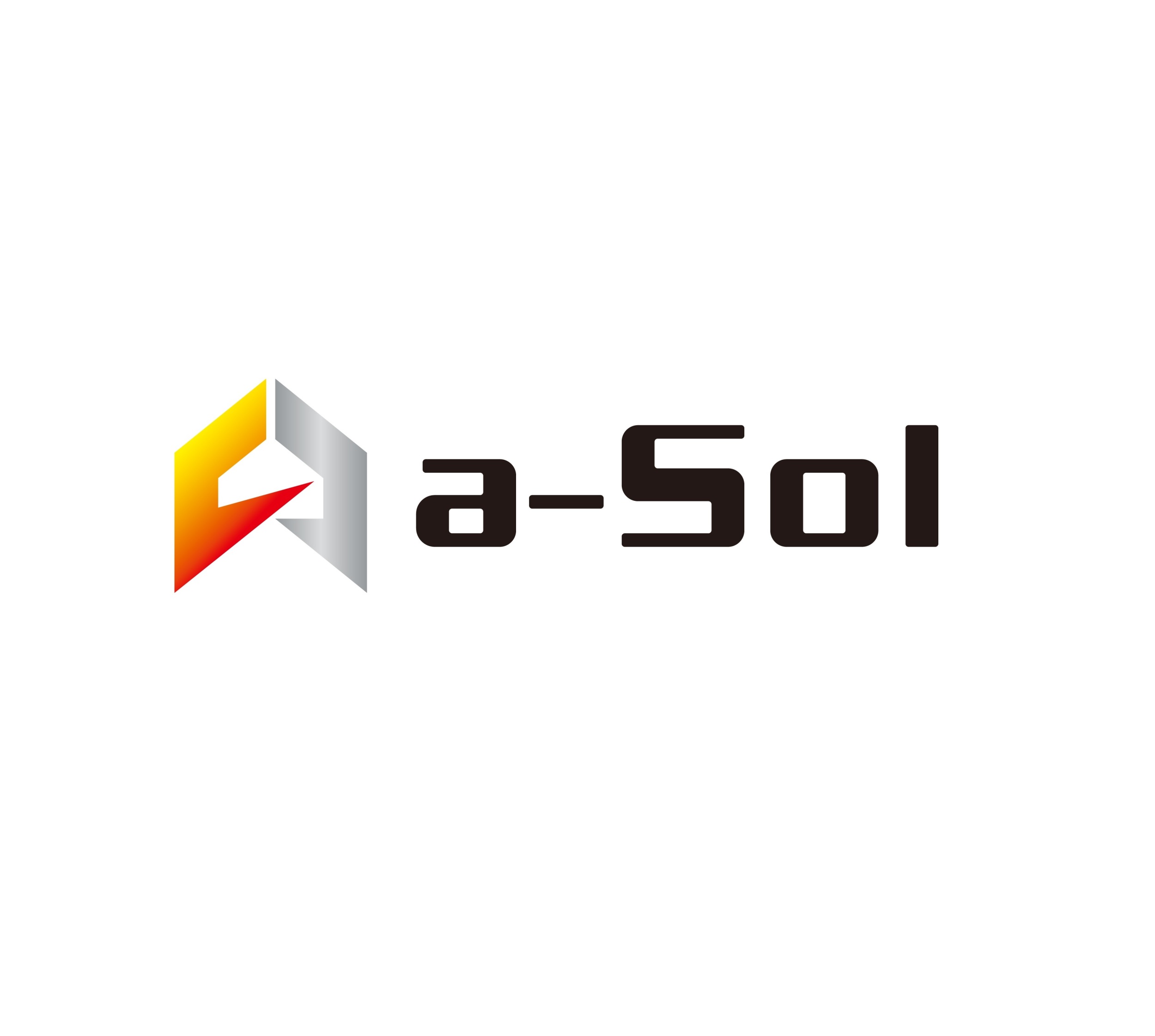