こんにちは!
カイゼン研究会の宇賀です。
今回のテーマは「結果を数値で管理。ではなくて」です!
現場を管理する指標がどこの工場のもありますよね。
品質不良、生産出来高、出荷数、生産性、在庫量などなど、これらの結果指標を1日、週、月、年などに区切って管理し結果的に良くなったかを判断していきます。
これこそが現場を管理すること。となっている工場はたくさんあります。
しかし、カイゼンを進める中で本当に大事なものは、結果管理ではなく、状態管理です。
もちろんトヨタでも膨大な工数をかけて、結果データを取り管理されているのですが、状態を管理していく中で、結果に表れていくという使い方です。
じゃあ状態管理って何なの?ということですが、プロセスの管理、基準(ルール)の管理です
以前、管理監督者の仕事は何かということで基準を作り、基準を守らせ、基準を変えるということを書きましたが、これらの仕事をできているのか?という経営管理になります。
そしてこの状態管理を、結果よりも優先するということを徹底してきたのがトヨタです。
フォードもGMも、数値結果、目標達成率を本社から集中的に管理し、そのKPI管理手法の結果、良い経営ができているということになっていました。
当時(需要に供給が追い付いていなかった時代)この経営手法の成功からどこの会社でも使われ、今も続いています。
難しい目標数値を立て、それをクリアしていくということです。
それが生産現場にまで落ちてきて、その数値をもとに管理していくということが主流のやり方です。
生産現場の目標が量の達成ならこれでもよいのですが、経営者の方に聞くと変化に強い現場を作りたいという回答が多いのです。(需要が伸び続けることはない、大きく変動する前提で、利益をしっかり出す。)
そこでトヨタが一貫してやっているのがトヨタ生産方式を前提とした、状態管理です。
これは何かというとジャストインタイムにしても、自働化にしても、1個流しにしても突き詰めれば、永遠に達成できないように見えることをあえて掲げています。
それを前提としてどうやってその状態に近づけるかというのが日々の仕事になってきます。
それに近づこうとするためには何が妨げになっているのか?
それを取り除いていくというのが現場の仕事で最も優先されていることです。
じゃあ近づくためには何が必要なのか?を考えたときに実現を妨げている問題を絶対に見落とさない、絶対に迂回して、回避しないことです。
そこに着目して発展してきたのがトヨタ生産方式における見える化のツールです。
(かんばんやアンドン、生産管理板など)
これらのツールを導入する目的はツールとその使い方を詳細にルールで決め(誰が、どこで、いつ、何をする)問題を回避できない環境を作っていることにあります。
そうでないと生産現場の仕事(障害を取り除くこと)が進みません。
そして現場の共通の認識として数値目標ではなく、より明快なジャストインタイム、自働化、一個流しといった、理想に近づくことが優先されています。
数値目標とは別にトヨタ生産方式という憲法を守ることが前提なのです。
それを守っているかを管理するということを徹底しているのが状態管理となります。
これらのツールや基準は最終的には理想に近づくためのツールです。
なので詳細にルールを決め導入するのですが導入しても、うまくいかない、これが障害でそのルールは守れないと声があがるのが、普通です。(忙しいなど工数以外の理由)
そして、そのためにやっているのです。
(全く問題なく、運用できてしまうと意味がない)
すべて現状把握のために導入しているので、これが原因でできませんでした、で終わるとその価値が今出ているのに、ということになるのです。
(導入することが目的になっている)
何か達成したい状態があり基準を導入するはずです。
導入してからが、どれだけ守れているか?守れない、導入できないのは何が妨げているか?を頻度を決めて観察し、記録します。
そこが次に取り組むことになっていくのです。
作った基準に対して、観察、チェックをルール通り管理監督者が行って次のステップにつなげているかというのを管理していくことが状態管理です。
(トヨタでさえほっておいてはできないので、朝会や日報など状態管理をする仕組みを作って管理している)
逆に結果管理だと数値しか見られていないため、問題を回避し放題なのです。
量が達成できない状況に追い込まれる状況では、うまく回るのですが他の変化では、行動のトリガーがない状態になってしまってカイゼンが進まない仕組みとなります。。
生産計画一つとっても生産計画の達成率で測定するのか
生産順序の順守率を見るのかで、見つけれる問題の量が変わります。
達成率だと総量が合ってればよいので問題が回避しやすい。
しかし、もともと立てた順序が守れないというのは部品納入や行内物流などが影響している可能性があります。
長くなりましたが問題を逃がさない、迂回しないために(異常を発見するために)見える化をしていきます。
じゃあ、導入した際は「できる?できた?」ということを聞き正常(Yes)、異常(No)、Noは何が妨げているの?というとこまでを日々データとして抑えたうえで次にすることを決めるというところまでが見える化の運用、導入になります。
ここをしっかり管理すること
つまり
状態管理を日々行うこと、そしてその積み重ねを守っているという前提で結果を管理すること、その優先順位で進める。
ということを書いてきました。 最後までお読みいただきありがとうございました!
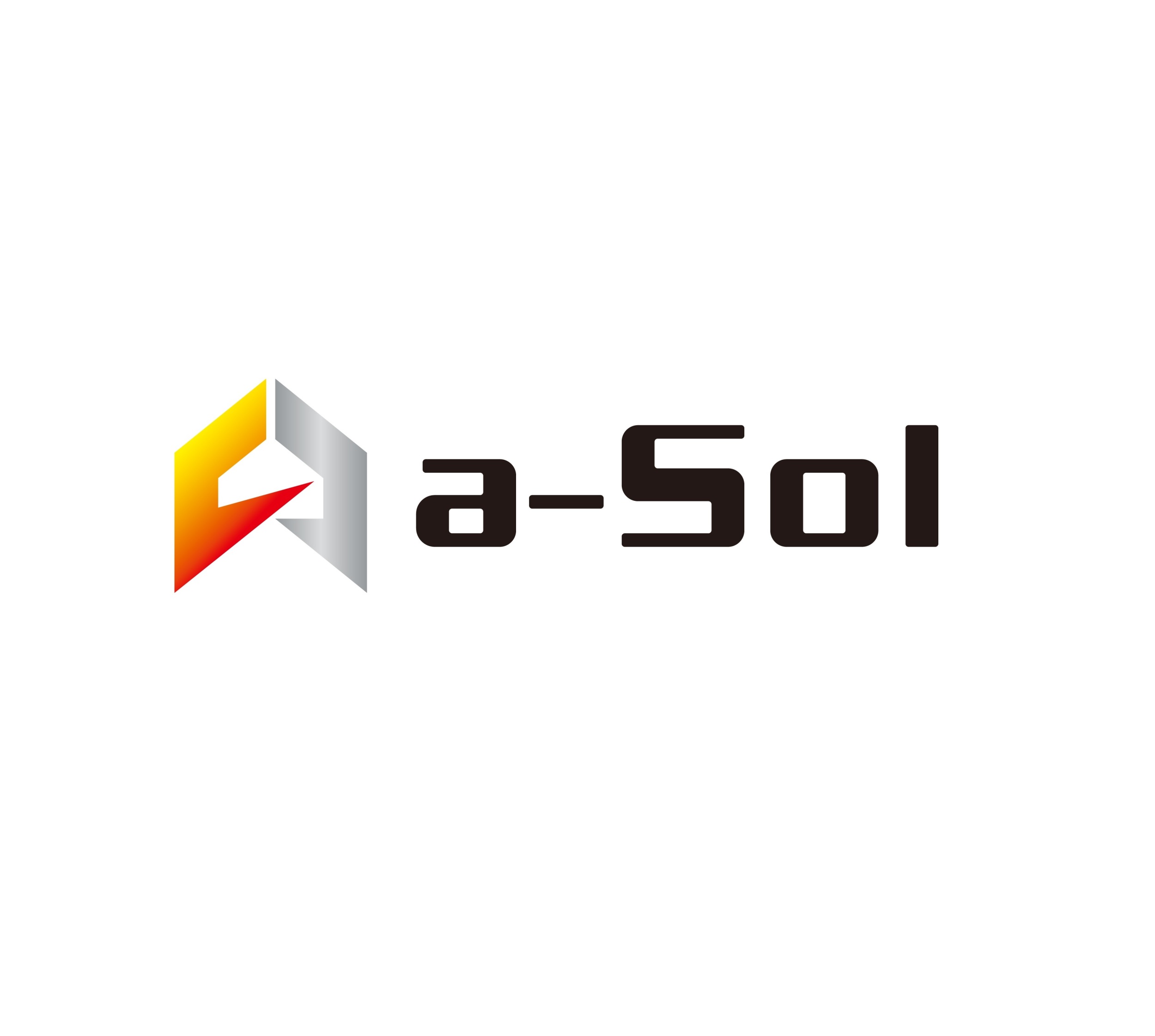